In the dynamic world of automotive manufacturing, innovation is a driving force behind enhanced efficiency and quality. The latest breakthrough comes in the form of advanced auto parts moulds, which are set to redefine the industry's production capabilities. These state-of-the-art moulds promise increased precision, improved durability, and streamlined manufacturing processes, raising the bar for automotive manufacturers worldwide.
Auto parts moulds are vital components in the production of various automotive parts, ranging from intricate interior components to robust exterior body panels. They serve as the foundation for creating precise and consistent shapes with remarkable efficiency. With advancements in design and technology, these moulds have become indispensable in the pursuit of automotive excellence.
One of the key features of these advanced auto parts moulds is their ability to create complex shapes with unparalleled precision. Utilizing computer-aided design (CAD) software and computer numerical control (CNC) machining techniques, manufacturers can develop intricate moulds that accurately replicate the desired specifications of the auto parts. This precision ensures a seamless fit and optimal functionality of the final products, contributing to overall vehicle performance and safety.
Furthermore, the durability of auto parts moulds is paramount in ensuring consistent production output. Made from high-quality materials such as hardened steel or aluminum alloys, these moulds can withstand the rigors of high-pressure injection molding processes. This longevity translates into extended tool life, minimizing downtime for maintenance and reducing production costs.
In addition to precision and durability, the modern auto parts moulds have been designed to optimize manufacturing efficiency. Manufacturers can now integrate advanced cooling systems within the moulds to accelerate the cooling process, resulting in faster cycle times and increased production output. This enhanced efficiency enables automotive manufacturers to meet growing demands while maintaining product quality and reducing lead times.
The integration of automation and robotics has also revolutionized the production process. Auto parts moulds are now equipped with sensors and actuators that interact seamlessly with robotic systems, allowing for the automated extraction of finished parts from the moulds. This automated process not only reduces labor costs but also minimizes the risk of human error, ensuring consistent quality in every part produced.
The advent of auto parts moulds has not only streamlined manufacturing processes but has also had a positive impact on environmental sustainability. Manufacturers can employ recyclable materials in the moulds, reducing waste and promoting a greener approach to automotive production. Additionally, the efficient use of resources and energy optimization in the manufacturing process further contributes to a reduced carbon footprint.
As automotive manufacturers strive to meet the evolving demands of the industry, the adoption of advanced auto parts moulds is becoming increasingly prevalent. These cutting-edge tools enable manufacturers to produce high-quality, precisely engineered auto parts in a cost-effective and sustainable manner.
The automotive sector's reliance on auto parts moulds is expected to continue growing in the coming years, with a focus on continuous improvement and innovation. As the industry embraces these transformative technologies, consumers can anticipate vehicles with superior performance, increased safety, and enhanced aesthetics, setting new standards for the automotive landscape.
In conclusion, auto parts moulds have emerged as the backbone of automotive manufacturing, empowering manufacturers with precision, durability, and efficiency. With their significant contributions to quality control, production optimization, and sustainability, these advanced moulds are set to shape the future of the automotive industry, driving innovation and excellence in every vehicle produced.
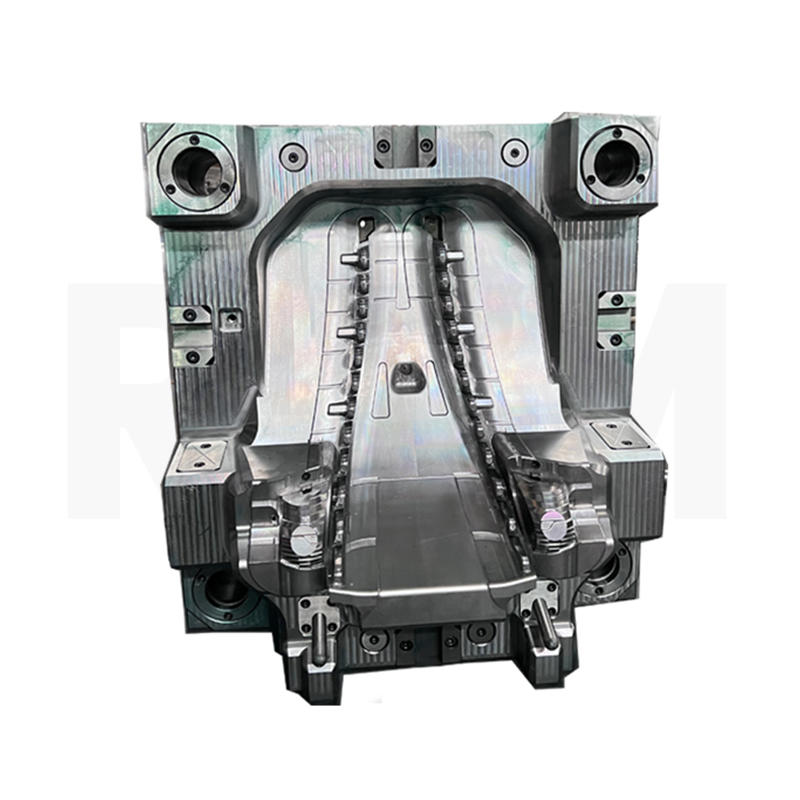