In the world of paint container manufacturing, the paint bucket mould is a vital component that ensures efficiency, precision, and consistency in the production process. These molds play a crucial role in shaping the durable and functional containers that hold various types of paints, coatings, and other liquid products.
Paint bucket molds are specifically designed to create the distinctive shape, size, and features of paint containers. They are typically made from high-quality, durable materials such as steel or aluminum to withstand the high pressure and temperature involved in the injection molding process. The molds are carefully crafted to deliver precise dimensions, smooth surfaces, and structural integrity to meet the stringent quality standards of the industry.
The process of manufacturing paint bucket molds involves a combination of engineering expertise, advanced technology, and meticulous attention to detail. It begins with the design phase, where skilled mold designers utilize computer-aided design (CAD) software to create a 3D model of the mold. This allows for precise measurements, intricate detailing, and the incorporation of specific features such as handles, lids, and pouring spouts.
Once the design is finalized, the mold production process begins. The chosen material, typically steel or aluminum, is carefully machined and shaped using computer numerical control (CNC) techniques. This ensures the precise replication of the mold design, including complex features and contours. The mold is then subjected to heat treatment processes to enhance its hardness and durability, ensuring longevity in the manufacturing environment.
The paint bucket mold plays a pivotal role in the injection molding process, where molten plastic material is injected into the mold cavity and cooled to form the final paint container. The mold's design, including the gate system, ensures proper flow and distribution of the plastic material, resulting in uniform wall thickness, smooth surfaces, and accurate shape. The precision of the mold guarantees consistent quality across each manufactured paint bucket, meeting the industry's strict requirements.
Furthermore, paint bucket molds offer versatility and customization options for paint container production. Manufacturers can create molds to produce paint buckets of various sizes, capacities, and designs to cater to specific customer needs. This flexibility allows for the production of a wide range of paint containers, from small cans for hobbyists to large buckets for industrial applications.
The efficiency and reliability of paint bucket molds contribute to streamlining the production process. With the ability to create multiple paint containers simultaneously, these molds significantly increase productivity and reduce manufacturing time. The repeatable and consistent results ensure minimal waste and optimize resource utilization, resulting in cost savings for manufacturers.
Additionally, paint bucket molds enable the production of containers that meet industry standards for safety and functionality. They are designed to ensure proper sealing, preventing leakage and evaporation of paint or other liquids. The precise molding process guarantees that the containers are sturdy and durable, capable of withstanding the weight of the contents and the rigors of transportation and storage.
In conclusion, the paint bucket mould plays a vital role in the efficient and precise production of paint containers. These molds, crafted with engineering expertise and utilizing advanced technology, enable the creation of durable, functional, and aesthetically pleasing paint buckets. With their ability to deliver consistency, versatility, and customization options, paint bucket molds contribute to the seamless manufacturing of high-quality paint containers that meet industry standards. As the demand for paints and coatings continues to grow, paint bucket molds will continue to be a cornerstone in the paint container manufacturing industry.
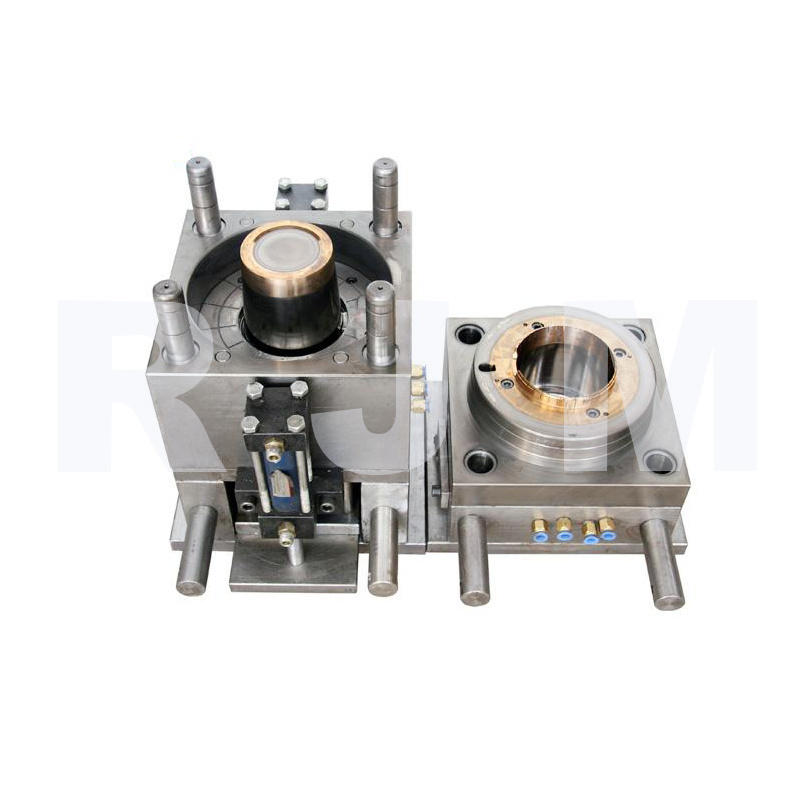