The painting industry is witnessing a transformative development with the introduction of advanced paint bucket moulds. These innovative moulds are revolutionizing the way paint containers are manufactured, offering increased efficiency, improved functionality, and enhanced precision. With their cutting-edge features, the paint bucket moulds are set to elevate the standards of quality and convenience in the painting process.
The paint bucket moulds incorporate state-of-the-art design and manufacturing techniques to ensure superior functionality. One of the standout features is the integration of a secure and leak-proof sealing mechanism. By employing precise sealing mechanisms within the mould, manufacturers can produce paint buckets that prevent leakage during transportation and storage, eliminating the risk of spills and waste.
Furthermore, the moulds facilitate the creation of paint buckets with ergonomic handles, ensuring comfortable grip and ease of use. These specially designed handles provide a secure hold, allowing painters to carry and pour paint with confidence, reducing the likelihood of accidents and ensuring a smooth painting experience.
Precision is a critical aspect of paint bucket moulds, guaranteeing consistent dimensions and accurate capacity. The moulds utilize advanced computer-aided design (CAD) software and high-precision machining techniques to create buckets that meet exact specifications. This precision ensures accurate measurements of paint quantities, enabling painters to estimate their needs accurately and minimize paint wastage.
Efficiency is another key advantage offered by paint bucket moulds. The moulds are designed to optimize the production process, allowing for high-speed injection molding and rapid cooling. This efficiency enables manufacturers to meet the growing demand for paint buckets while maintaining consistent quality and reducing production time. The streamlined production process also contributes to cost savings and enhanced productivity for manufacturers.
The versatility of paint bucket moulds is a significant advantage for the painting industry. Manufacturers can create buckets in various sizes and designs, catering to different painting requirements. Whether for large-scale industrial applications or small DIY projects, the moulds can produce paint buckets that suit diverse needs, offering flexibility to painters and consumers alike.
Moreover, the paint bucket moulds are often made from durable materials such as high-density polyethylene (HDPE) or polypropylene (PP), ensuring robustness and longevity. These materials make the buckets resistant to chemicals, impact, and extreme temperatures, providing reliable storage solutions for various types of paints and coatings.
The environmental impact of paint bucket production is also being addressed by the paint bucket moulds. Manufacturers are increasingly incorporating recyclable materials and adopting eco-friendly production practices. This shift toward sustainability aligns with the industry's growing emphasis on reducing plastic waste and promoting a circular economy.
As the demand for paint bucket moulds continues to rise, the industry is witnessing ongoing advancements and innovations. Manufacturers are exploring new materials, technologies, and design possibilities to further enhance the functionality and efficiency of these moulds, ultimately benefiting painters, consumers, and the environment.
In conclusion, the introduction of advanced paint bucket moulds is reshaping the painting industry, revolutionizing the production of paint containers. With their focus on functionality, precision, efficiency, and sustainability, these moulds offer a new level of convenience and reliability for painters and consumers. As the industry embraces these technological advancements, the painting process is poised to become more efficient, precise, and environmentally responsible, setting new standards for the future of painting.
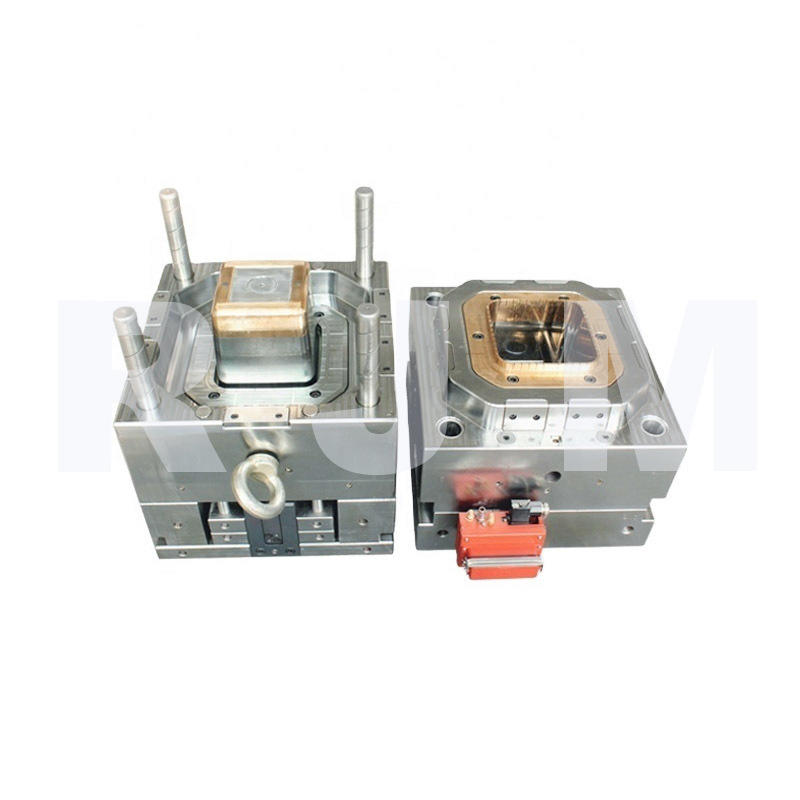